As technical remedies to climate change go, taking carbon emissions out of passenger transportation is easy; we can switch from gasoline engines to electric motors fueled by renewable energy sources.
In contrast, “decarbonizing” heavy freight carried by trucks is hard. No technology today has the power and efficiency to replace diesel engines for moving goods over long distances by land and sea, which is unfortunate because society’s increased shipping demands are driving up diesel consumption.
Researchers at the University of Virginia’s School of Engineering and Applied Science are taking on the challenge to discover which diesel fuels burn cleanest, under what conditions and with the fewest offsetting environmental costs. Their particular focus is minimizing production of nitrous oxide, or N2O.
William S. Epling, professor and chair of chemical engineering, is leading the effort with co-principal investigators Lisa Colosi-Peterson, an associate professor in the Department of Engineering Systems and Environment, and Chloe Dedic, an assistant professor in the Department of Mechanical and Aerospace Engineering.
Also contributing as senior investigators are Robert Davis, William Mynn Thornton Professor of Chemical Engineering, and Chris Paolucci, assistant professor of chemical engineering.
The project is supported by a $1.7 million grant through the Environmental Convergence Opportunities program of the National Science Foundation’s Division of Chemical, Bioengineering, Environmental and Transport Systems. The program requires that research team members have disparate expertise and perspectives to find imaginative solutions to difficult and pressing societal challenges.
So, for this funding, even before team members can grapple with solving the technical problem, they have to find common ground on the research questions – amongst a group of people whose expertise and perspectives are, by design, different from one another.
“That was harder than you might imagine it to be, but it was hard on purpose,” said Colosi-Peterson, an environmental engineer who joined the team because she recognized that diesel engines aren’t going away any time soon. “I think the NSF is very clever to have such a big incentive, because it took a lot of thinking to come up with something that really leveraged all our individual skills and interests.”
Colosi-Peterson is an expert in life cycle assessment, a computer modeling-based area of study that examines the environmental price tag of the products, processes or services people use. Dedic studies combustion and reacting flow systems, and is a rising star in the development of new laser-based techniques for nonintrusive measurements of the complex chemical reactions and fluid dynamics that occur during combustion. Epling is well known in his sphere of catalysis, especially for his work to reduce pollutants emitted from diesel engine exhaust systems.
The Technical Problem(s) Explained
When fuel – whether biomass- or petroleum-based – is combusted, not all of it is burned. The exact chemical composition of the leftover hydrocarbons depends upon numerous factors, including fuel type. To meet Environmental Protection Agency vehicle emissions regulations, the catalytic converter in your car and the after-treatment systems used in diesel semi-trailer tractors clean those exhaust gases through chemical reactions after they leave the engine.
What eventually comes out the tailpipe at any given moment also depends on variables such as whether the engine is hot or cold, how effectively the air and fuel mixed in the engine, and the age of the catalyst material, which loses efficacy over time. The team is looking broadly at these emissions, including carbon dioxide, methane and particulate soot, but the primary target is N2O.
Here’s the thing: N2O is not made in your engine.
“It’s made over your catalytic converter, which is supposed to clean up the exhaust gas. What we want to do is understand how a diesel catalytic converter makes N2O, as a function of the fuel type,” Epling said. “If we know what hydrocarbons lead to the most or least N2O being made, then we can think about what is the right type of fuel that minimizes how much N2O is made.”
Why the focus on N2O? The EPA, historically more concerned with air pollution than climate change, only began regulating N2O for diesel exhaust in 2011 after numerous studies showed the gas’ global warming potential, which scientists call GWP, to be 298 times greater than carbon dioxide. That’s because N2O traps more heat than other greenhouse gases.
Carbon dioxide is still the biggest greenhouse gas contributor from diesel because of how much is exhausted, said Carlos Weiler, a Ph.D. student in Epling’s lab who is running the catalysis experiments for the project. The industry also doesn’t have a good way of mitigating N2O production.
“And so, we have to look at the other products that are formed,” Weiler said. “They’re all destructive to the environment in some way, but in terms of the global warming potential of diesel exhaust, N2O is pretty potent.”
The Team’s Approach
Weiler will run experiments using different fuel inputs and catalyst combinations working under advisement from Epling and Davis, another widely recognized catalysis expert. Essentially, the unburnt hydrocarbons from combusted fuel will go into a catalytic reactor that simulates a diesel after-treatment system, and Weiler will measure what gases come out. Weiler will feed his results to Sugandha Verma, a graduate student in Paolucci’s computational catalysis group, who will use computer simulations of catalytic reactions to predict outcomes and suggest further lab experiments.
But understanding how N2O is made by the catalytic converter, or how much, requires knowing what hydrocarbons leave the engine. That’s where Dedic comes in. Measuring what’s left of a fuel after engine combustion is difficult because the compounds are structurally very similar. Traditional spectroscopy, which relies on how light interacts with various molecules, struggles to distinguish one hydrocarbon from the next. There are techniques to count the number of carbon and hydrogen molecules, but that entails removing gas samples from the engine during combustion, potentially changing the chemistry.
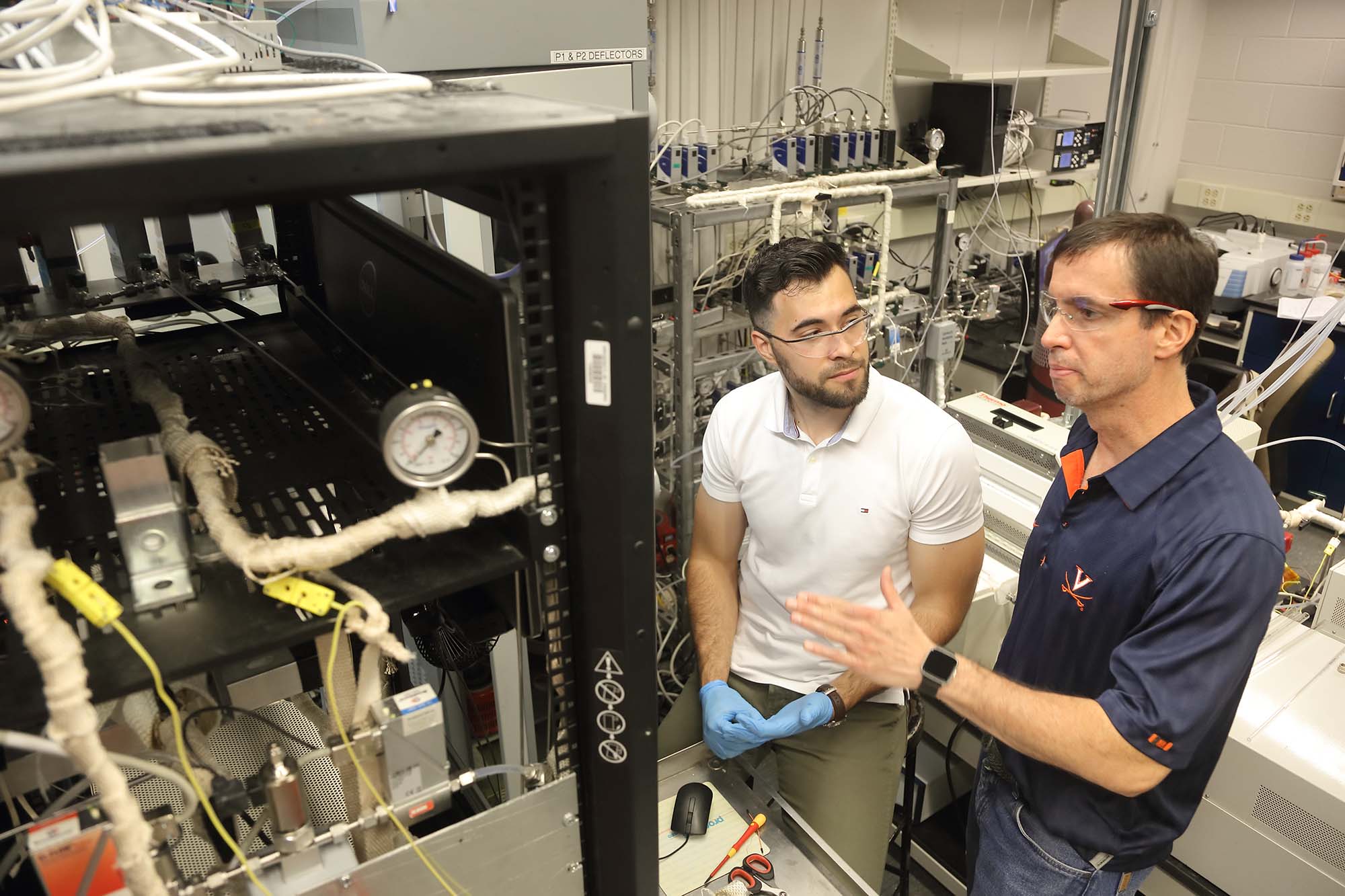
Ph.D. student Carlos Weiler, left, is running the experiments on various types of diesel fuels in the environmental catalysis lab of professor of chemical engineering William Epling, right. (Photo by Tom Cogill)
“The best-case scenario is taking a measurement without interrupting the sample where the reaction is happening,” Dedic said. “Then you’re getting a true measurement of what’s occurring within your reactor.”
Dedic is approaching these challenges from two angles. First, her team is designing a simplified reactor – a burner that can safely combust liquid diesel formulations in the lab – to isolate the combustion chemistry from other engine effects, such as fluid dynamics. The second is using ultrafast laser sources to develop new measurement techniques for the project.
“We want to probe these molecules on the same time scales that they’re reacting and colliding with one another. We can observe molecular vibrations and rotations in time to provide more information than you get from traditional frequency-resolved spectroscopy,” Dedic said.
The Bigger Picture
While Dedic’s lab identifies diesel products for Epling’s team to experiment with, Colosi-Peterson’s life-cycle assessment group is taking a systems approach, designing models to use the lab data to predict the costs of implementing the fuels in the real world. For example, if biomass-based diesels produce less N2O, how much agricultural or carbon-capturing forest land would be lost to fuel production? How much energy will we expend to grow biofuels, and where will that energy come from? Another important question Colosi-Peterson will examine is whether reducing N2O from diesel emissions even matters, or is it insignificant relative to the effects of other pollutants?
The project sets up a back-and-forth dynamic between the experimentalists and the modelers to better integrate the three research groups, which ordinarily would do their work independent of each other. It’s a more proactive approach to improving the environmental performance of new technology in development, Colosi-Peterson said, rather than waiting for the technology to come along, and then assessing its societal cost.
“Bill and Chloe might say, ‘Here’s a couple of things we’re thinking of doing,’ and I put all of that data into my model, and say, ‘Well, here’s what would happen if we did that at large scale. Is there any way you could make this part of the process a little bit less emitting?’
“And so I think that this desire to work more closely together during the bench scale is meant to cut out some of that trial and error and to be more intentional about the kinds of fundamental science that Bill and Chloe do.”
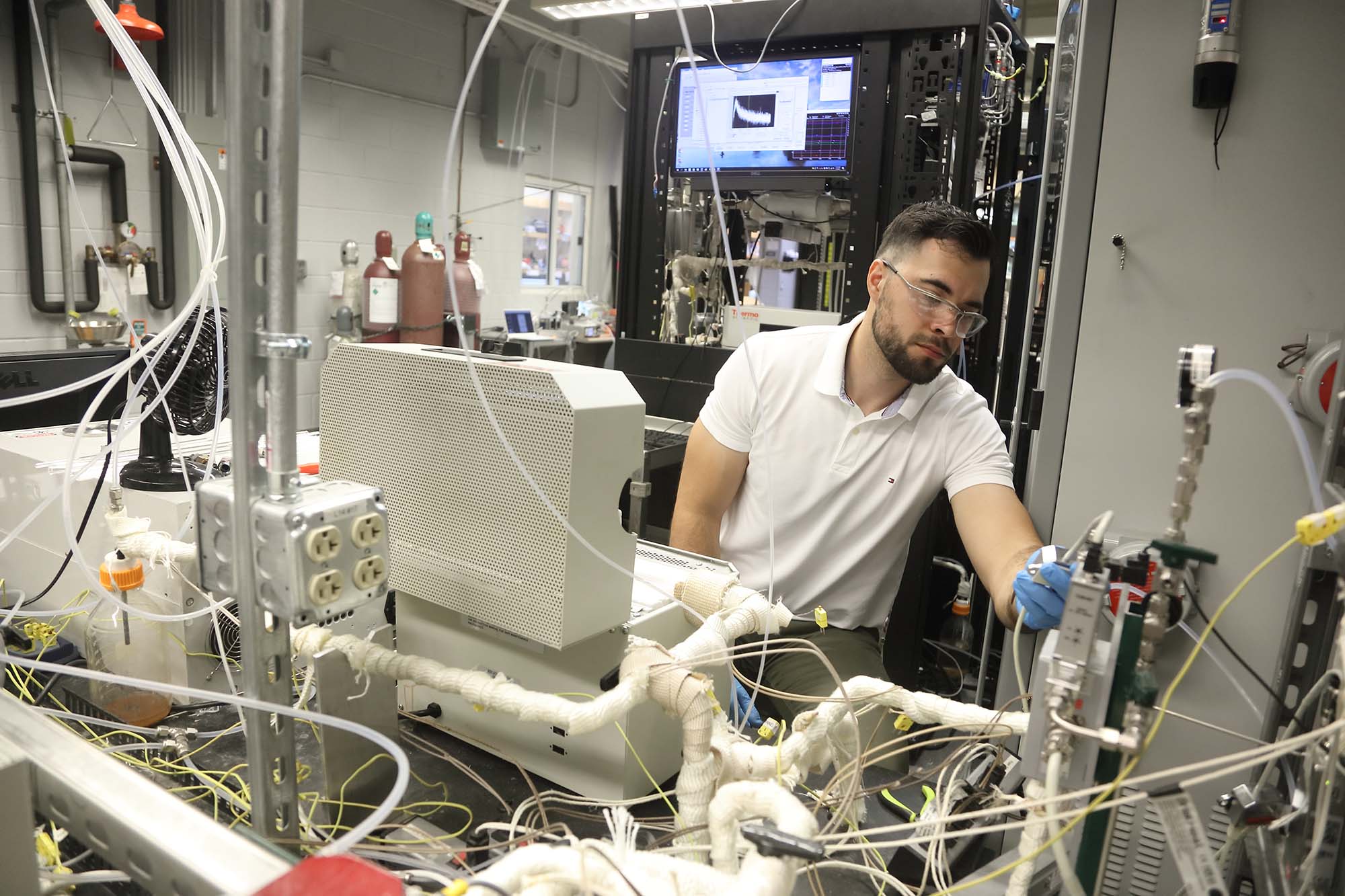
Chemical engineering Ph.D. student Carlos Weiler is running the experiments on various types of diesel fuels in professor of chemical engineering William Epling’s environmental catalysis lab. (Photo by Tom Cogill)
The team’s research will be exacting in its science, but holistic in its approach, Epling said, referencing the project’s title, “A holistic effort to decarbonize diesel for heavy duty transportation: Targeted combustion and exhaust catalysis research to improve life-cycle performance.” He hopes the collaboration will lead to more nuanced policy-level understanding of to what extent proposed strategies – such as a regulation to reduce N2O emissions from diesel engines – can deliver meaningful global warming improvements.
One way policy may ultimately be improved is through the cross-training of the students collaborating on the project, who are just beginning their Ph.D. studies, Colosi-Peterson said.
“It’s really powerful when the student making the catalyst and running reactions in the lab is confronted with questions about the difference their technology will make, or its consequences,” she said.
“Conversely, Bill or Chloe may challenge some of the values my students are using in their systems-level analyses, in effect ground-truthing the assumptions we make when we build models for policy formation and legislation. I think there’s a lot of benefit in students having to think at the bench scale and at the systems level.”
Media Contact
Article Information
December 20, 2021
/content/diesel-engines-move-goods-around-globe-uva-engineers-work-curb-emissions